
Torque Converter Tech Tips
- Author: Ed Lee
Maintaining the proper centerline during the torque-converter rebuild process is very important. How well the centerline was maintained during the process can be measured by how much balance weight needs to be added at the end of the process.
The original-equipment manufacturers (OEMs) do a good job of maintaining the centerline when they build the torque converter. If the converter is indexed properly, the aftermarket rebuild should require about the same amount of weight to rebalance. If the converter requires significantly more weight to rebalance, the rebuild process should be inspected for centerline issues.
Balancing basics tell you that you are adding weight on one side of the converter to offset a heavy spot on the opposite side of the converter. If you haven’t added any weight to the converter, where did the heavy spot come from? The answer is that either you are compensating for weight that was removed from the converter during a machining process or you are compensating for an off-center condition.
The centerline issues that affect the balance process may start as early as the parting procedure. When a converter is not piloted properly while being cut open, more metal must be removed from one side of the cover or impeller to separate the unit.
In Figure 1, a Chrysler pilot sleeve was mistakenly used when this GM converter was parted. The loose piloting allowed an off-center condition that resulted in one side of the cut converter being much thinner and lighter than the opposite side. If these components are reused, the converter will require more weight to rebalance.
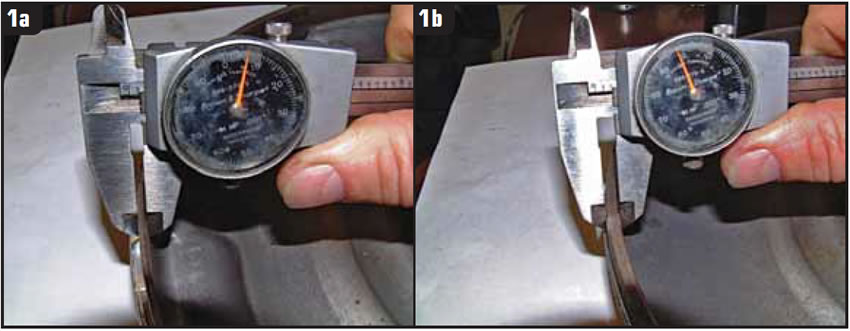
The centerline issues continue into the preparation processes. The cover and impeller need to be centered properly when they are machined for clearance. If the impeller is going to have a new hub welded in place, efforts must be made to keep the new hub concentric with the centerline. Even a few thousandths inch off center at any step will mean several grams of extra weight to rebalance.
The welding and balancing processes are next to come under scrutiny, and both have centerline issues that involve the converter pilot. The turntables on the welder and balancer each rely on some sort of collet or sleeve to center the converter. Any wear to the collet, sleeve or the pilot itself will dramatically affect the balance process. The amount of imbalance will vary with the weight and diameter of each converter.
For example, a 45-pound converter 12 inches in diameter will need almost 31/4 grams of added weight for each 0.001 inch that the converter is off center. The heavier and larger-diameter converters will need even more weight to compensate for any off-center conditions. For accuracy, each pilot should be measured individually in at least two places with either calipers or micrometers. You should never rely on a go/no-go gauge to check a pilot.
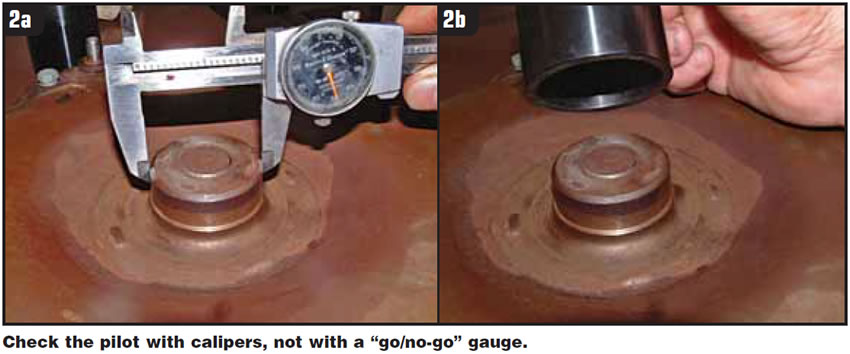
Following your shop-equipment manufacturer’s routine-maintenance schedule is also very important. This includes checking the runout on your welder and balancer at regular intervals. Tools and equipment that are worn out or are out of calibration can cause multiple issues.
Rebuilding a torque converter is a lot like building a house. If you start with a good foundation, you will have a much better chance of ending up with a quality product. If you pay attention to keeping all the components in a torque converter concentric, perpendicular and parallel as required, you will find that you won’t have to compensate by adding large amounts of balance weight to your finished product.

Ed Lee is a Sonnax Technical Specialist who writes on issues of interest to torque-converter rebuilders. Sonnax supports the Torque Converter Rebuilders Association. Learn more about the group at www.tcraonline.com.